GOVERNMENT SHARED SERVICES CENTRE
“We tried applying Lean our own but struggled to make it relevant to our day to day work. Deploying ServiceForce, Expertivity’s Lean Management System, transformed our ability to execute our work and provided a platform for continuous improvement.”
Facts
- Overall Capacity – Up By 22%
- Daily Work-In-Process – Down By 37%
- Work Volume – Up By 7%
Results
- Teams Enhanced Their Lean And Operations Management Capabilities
- Deployed Lean Management System, ServiceForce
- Continuous Improvement Framework
- The Day-To-Day Experience For The Staff Improved
- The Process Laid The Foundations For Expansion
Award Winning Results!
These and other similar results helped us win Lean Service Provider of the Year 2019
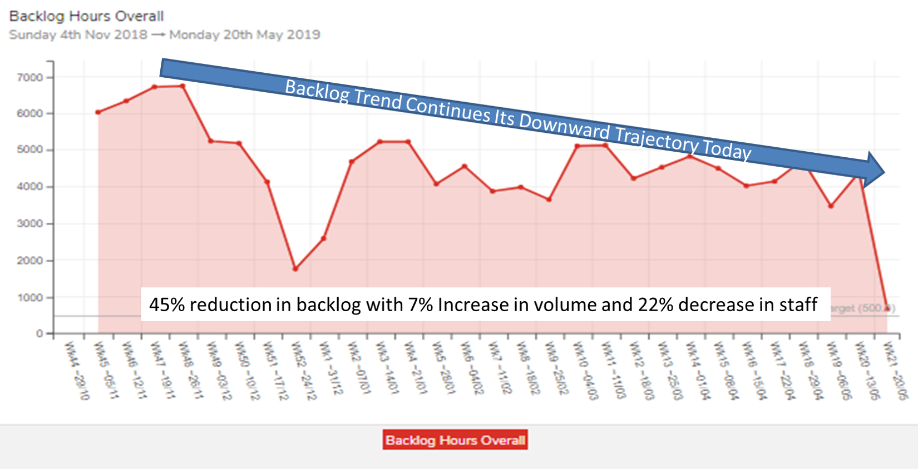
What was at stake?
The governments shared service centre employs over 700 people across 6 sites and provides HR, pensions and payroll administration services for 39 Government Depts., and 52 public service organisations totaling 124,000 people. The client was tasked with improving the service to customers while leveraging the economies of scale expected from a shared services model. To help scale their operations management throughput, the client had already attempted to pilot the application of Lean Six Sigma but had struggled to make them relevant to their day to day operational challenges.
What was the result?
Expertivity worked with the teams to enhance their Lean and Operations Management capabilities and deployed our Lean Management System, ServiceForce, to provide additional operational insights and help manage their day to day demand and capacity requirements. During the program, the teams reduced their daily work-in-process (WIP) by 37% and their overall capacity requirements by 22% while their work volumes increased by 7%. The newly acquired skills along with the enhanced data made available via ServiceForce allowed the team to identify additional process improvement opportunities more than the gains already achieved.
Background
The shared service Centre was achieving good service levels but were concerned with their ability to scale their operations and take on additional work with the same resources. While the initial focus was on successfully transitioning work out of the businesses and into the service Centre and free up resources in the business, the focus had now turned to the centre's ability to optimise its processes and scale efficiently.
The challenges:
Expertivity helped the organisation focus on three objectives to help them attain their goals. First, they needed to bring the day to day management of their workload under greater control. To do that they needed help to enhance their existing operations management capabilities and access to better operations management tools and data.
Second, they needed to increase their people’s awareness of the principles behind Lean and how it could help them address the root causes of much of the low value work created by some poor processes. The traditional government and public sector management culture relies on day today instructions being delivered from management “down” to the workforce. Apart from its negative impact on workforce engagement, it ties the managers time up with day to day micromanagement activities. While the managers understood the need to improve the frontline staff’s engagement, they were lacking the necessary work management tools and data to empower their staff.
Third, they needed to equip their teams with the right problem-solving skills. While the frontline people were comfortable describing issues, they didn’t feel they had the power to solve them. The management team wanted to address the problems as close to their origins as possible which required developing problem-solving skills in each team. The core tools required to address most problems encountered on a day to day basis are quite simple when applied in a structured manner.
What we did:
Our Service Operations Management Program is one of our most successful programs and has been developed and improved over the last 15 years. Recognising that most service and knowledge work is highly variable and often complex, our program consists of 2 x 2-hour sessions per week with each operations team and runs over 12-14 weeks. During that time, the teams complete 5 major milestones. The first two milestones contribute to building an effective demand and capacity management model of the teams work on ServiceForce. Milestone three introduces the team to daily work allocation processes on ServiceForce whereby work is optimally allocated across the team based on the skill soft e workforce and reasonable expectations are agreed for work completion. Milestones four leverages the data being developed in ServiceForce to target non value-added activities for reduction and elimination. Milestone five introduces the teams to inter-team improvement opportunities and sets the platform for end to end process ownership and improvement.
The outcomes:
The main objective of the program was to build a set of core operational excellence competences in the teams and provide each manager and team leader with the tools and operations management skills to manage their work more effectively and efficiently both locally within their own team and horizontally across the end to end business processes. It was expected that these investments in the teams would result in a 15% improvement in their effective work capacity which in turn would translate into a reduction in the teams WIP (work in process) levels.
During the program, the teams reduced their daily work-in-process (WIP) by 37% and their overall capacity requirements by 22% while their work volumes increased by 7%. The newly acquired skills along with the enhanced data made available via ServiceForce allowed the team to identify additional process improvement opportunities in excess of the gains already achieved. The organisation now has in place a work an Lean Operational Excellence management system that embeds their day to day work management within a continuous improvement framework.
The organisation now has in place a work a Lean Operational Excellence management system that embeds their day to day work management within a continuous improvement framework.